Switching CAD software
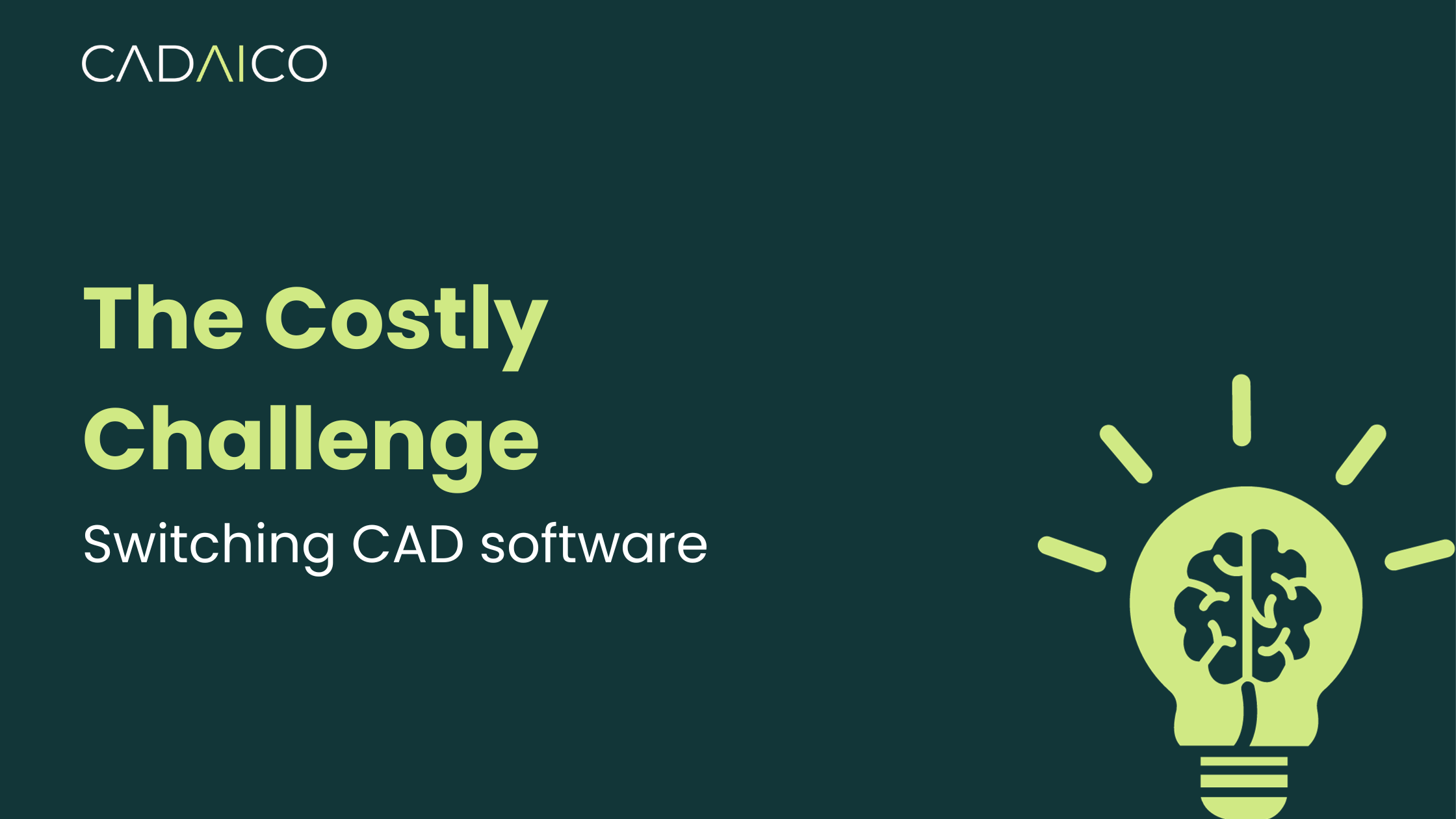
In the constantly changing world of engineering and design, Computer-Aided Design (CAD) software plays a crucial part in realising innovative ideas. These programs are the digital tools that engineers and designers use to create the products of tomorrow. Mid-sized and large companies like Festo and Daimler often find it difficult to keep up with the constant evolution and improvement of CAD software due to their reluctance to adjust their existing systems for every new update released by software companies.
CAD software updates often include new features to improve engineering efficiency, but transitioning to a new system can be daunting for well-established companies with established workflows. There are key reasons why companies hesitate to make these transitions, as suggested by both industry experience and insights from the Sales Director of a licensed PTC partner company in Germany.
These include exclusive functions and file formats. Each CAD program has its own particular abilities and file formats that generate specific data. This distinctiveness of each software distinguishes it from others and impedes easy replacement. Companies commonly depend on these special features that suit their particular requirements, resulting in a complicated process when switching software systems.
To show how big changes can be, let's look at Daimler, a huge company in the car industry. They used DS Catia for 25 years, but then switched to Siemens NX. This took five years and six thousand engineers had to be trained. They also had to change over 230,000 CAD files and over a thousand suppliers had to start using the new CAD software. The whole process was very expensive, costing a sum in the low hundreds of millions of pounds.
Daimler decided to do it for several reasons: soon there will be a software update - moving from Catia V5 to Catia V6 - and this will cause a significant change in the system. This upcoming update caused Daimler to consider their options.
- PLM/PDM Integration: Catia V6 obliged users to adopt its Product Lifecycle Management and Product Data Management systems. This posed a major challenge for Daimler, which had its own established PLM/PDM in place.
- Subversion Complexity: Daimler was handling a staggering 15 diverse subversions of Catia, causing inefficiencies and complexities in their design process. The consolidation to one CAD software became imperative.
In essence, the engineering sector is caught in a costly and ineffective cycle, where the CAD design method frequently stays stuck in the past. This problem calls for an up-to-date and effective solution, which is where CADAICO comes in.
CADAICO offers a new outlook and a revolutionary strategy to CAD design. By incorporating decentralized machine learning and blockchain technology, CADAICO simplifies and modernizes the CAD design process. CADAICO aims to guarantee that designs are accurate, simplify switching between CAD systems, and provide a modern solution to the challenges of CAD software transitions.
In a world where progress relies on innovation, CADAICO intends to unshackle engineers and designers from the limitations of traditional CAD software, inspiring them to create a more efficient, cost-effective, and innovative future. The problem with CAD software may continue, but a better and more effective solution like CADAICO is available.
Sources:
https://www.engineeringspot.de/2015/01/die-ganze-story-warum-daimler-auf-nx-wechselte/
https://blogs.sw.siemens.com/news/major-cad-overhaul-why-daimler-made-the-switch-to-nx/
https://www.cio.de/a/daimler-wechselt-catia-gegen-siemens-nx-aus,3231335